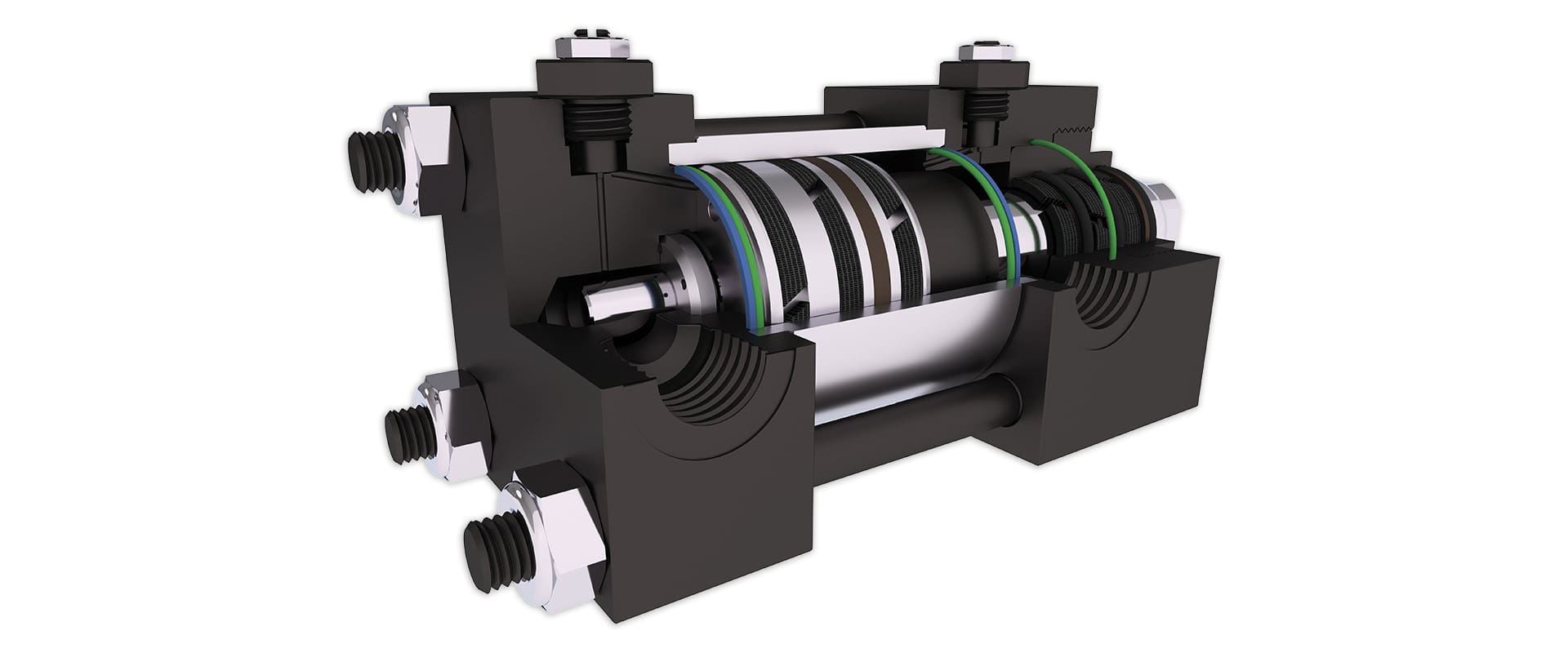
On some highly intensive applications, mold makers require high speeds from the components installed on the mold; of course, this includes hydraulic cylinders. But such high speeds (> 0.1 m/s) can be devastating for the piston; imagine being smashed against either the front or the cap of the cylinder without any kind of braking, several times per minute, and you can get an idea of the reduced lifespan of a product used like that.
The natural solution has always been including some kind of cushioning effect. And designers have really let their creativity run wild: some have put a sort of rubber cushion at either end to reduce the impact, some have set up convoluted hydraulic cushioning systems, often difficult to fine-tune at will. That is why we’re proud of our solution.
The base of our system is a standard hydraulic cushioning. Therefore, kinetic energy is absorbed by trapping oil in a virtually closed volume at the end of the stroke, which will let it out through a very narrow orifice. The increase in oil speed to the square generates a pressure drop, which absorbs the energy along the cushioning length. Then, of course, we have improved and built on this technology. How?
- Easy and precise adjusting of the cushioning effect. Cushioning screws are custom-made, with their cone set at a specific angle to allow very fine tuning.
- Safety against over-opening. The screw cannot be loosened past its safety limit due to the safety nut provided.
- Fast re-start in the opposite direction. The bushing will close oil passage when cushioning is needed, but will let oil flow through in the other direction.
One more thing: we have implemented our cushioning not only on standard ISO 6020/2 tie-rod cylinders, but also on selected compact block cylinders, like the V500 CZ, helping reach speeds up to 1 m/s, without breaking the piston to pieces.
Speed, with our cushioning, is not a problem anymore.